Как выбрать абразивный инструмент.
Маркировка абразивного зерна
Маркировка шлифматериалов - это комбинация цифр и букв. Согласно ГОСТу
28818-90 электрокорунд нормальный имеет следующие обозначения : 12А, 13А,
14А, 15А. Чем выше число в префиксе маркировки, тем выше качество
материала, т.е. выше твердость за счет меньшего количества ненужных
примесей и выше режущая способность материала.
Электрокорунд белый обозначается : 22А, 23А, 24А, 25А.
Качество материала во многом зависит как от чистоты исходного сырья,
так и от способа производства.
Источником электрокорунда белого является глинозем - высокоалюминистое
сырье, продукт обогащения бокситовых глин (98-99% оксида алюминия). Т.н.
альфа-глинозем - почти стопроцентное сырье высшей степени очистки.
Получение из глинозема абразива высшего сорта (25А), обладающего высокой
твердостью и высокой режущей способностью, достигается за счет более
высокой температуры плавления и более быстрого охлаждения расплава,
благодаря чему кристаллы абразива становятся более "лучистыми" и при этом
более твердыми. Вспомним, что режущая способность абразивного зерна
определяется количеством режущих вершин. Более твердое зерно является и
более хрупким, поэтому высокосортный абразив лучше подходит для шлифшкурки
и прочих изделий с абразивным покрытием, в то время как материал низшего
сорта более пригоден в качестве свободного абразива для пескоструйного
шлифования.
Можно вывести шкалу, связав сортность абразивов и область применения по
принципу : от 12А до 25А - от СВОБОДНЫХ АБРАЗИВОВ до ИЗДЕЛИЙ С АБРАЗИВНЫМ
ПОКРЫТИЕМ (ШЛИФШКУРКИ).
Зерно марок 13А-15А эффективнее использовать в кругах при высоких
ударных нагрузках, например в отрезных и обдирочных кругах на бакелитовой
связке, и в другом инструменте и операциях, подразумевающих высокое
давление на обрабатываемую поверхность и/или объемное снятие материала.
Более хрупкие марки 22А-24А эффективнее используются в кругах на
керамической связке. В шлифшкурке и прочих изделиях с абразивным
покрытием, работа которых не связана с высоким давлением и направлена на
прецизионную обработку поверхностей, используют хрупкий материал с высокой
режущей способностью марок 24А-25А.
Хром-титанистый электрокорунд обозначается 95А.
Циркониевый электрокорунд обозначается 38А. Шлифзерно обладает
уникальным сочетанием прочности и высокой режущей способности, поэтому
используется в кругах для обдирочных операций с высокими ударными
нагрузками и объемным съемом материала. Режущая способность в 10 раз выше
чем у электрокорунда нормального в аналогичных операциях.
Сферокорунд - ЭС.
Монокорунд - 43А-45А.
Карбид кремния черный -
52С-55С.
Карбид кремния зеленый - 62С -65С. Получение высокосортного
материала из карбида кремния, как в случае с электрокорундом, достигается
за счет повышенной температуры плавления и быстрого охлаждения.
Высокосортный абразив из карбида кремния используется в основном в
шлифшкурке.
Круги шлифовальные
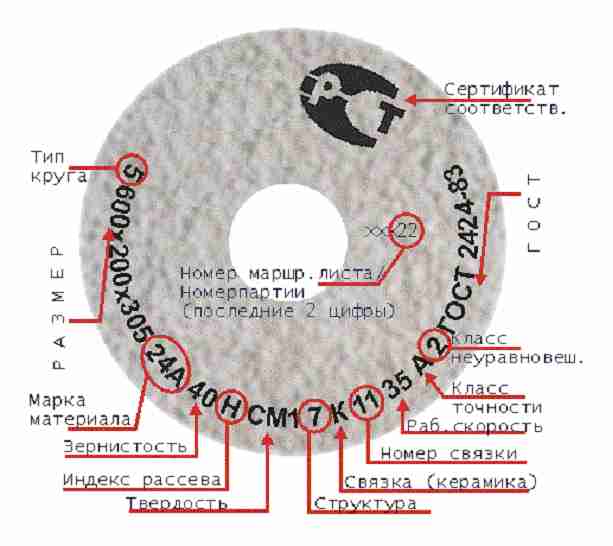
Зернистость |
Крупная |
Средняя |
Мелкая |
Тонкая |
320 (б)
250 (б)
200 (б)
160 (б)
125 (б)
100 (б)
80 (б)
63 (к, б) |
-
-
50 (к, б)
40 (к, б)
32 (к, б)
25 (к, б)
20 (к, б)
16 (к, б) |
-
-
12 (к, б)
10 (к, б)
8 (к, б)
3 (к, б) |
-
-
5
4
3
М63
М50
М40
М28 |
Твёрдость |
ВМ1, ВМ2 – весьма мягкая (к) |
М1, М2, М3 – мягкая (к, б)
|
СМ1, СМ2 – среднемягкая (к, б) |
С1, С2 – средняя (к, б) |
СТ1, СТ2, СТ3 – среднетвёрдая (к, б) |
Т1, Т2 – твёрдая (к, б) |
ЧТ1, ЧТ2 – чрезвычайно твёрдая (б) |
Шлифовальный материал |
14А – нормальный, (к, б), электрокорунд |
25А – белый (к, б), электрокорунд |
38А – циркониевый (б) электрокорунд |
93А, 94А, 95А, 96А – хромотитанистый электрокорунд (к, б)
|
53С, 54С – чёрный карбид кремния (к, б) |
63С, 34С – зелёный карбид кремния (к, б)
|
Связка |
Бакелитовая (б) |
Керамическая (к) |
Электрокорунд нормальный
Электрокорунд нормальный получают в электродуговых печах
восстановительной плавкой шихты, состоящей из бокситов, углеродистого
материала и чугунной стружки. Минералогическая основа бокситов - корунд
Al2O3 (не менее 60%) и гексаалюминат кальция CaO*6Al2O3. В процессе
восстановительных реакций примеси Fe2O3, SiO2, TiO2 переходят в
ферросплавы, кроме CaO.
Плотность - 3.85-3.95г/см3. Микротвердость - 18.9-19.6ГПа.
Электрокорунд нормальный - широко рапространенный материал,
используемый для изготовления инструмента и шлифшкурки с различными типами
связки. Используется и в свободном виде, для струйной обработки. Наиболее
эффективен при обработке углеродистых сталей, в опреациях шлифования,
резки и обдирки.
Электрокорунд белый
Электрокорунд белый получают плавлением глинозема в электродуговых
печах. Глинозем является продуктом обогащения бокситовых глин. Содержание
корунда в глиноземе 98-99% и 1-2% - алюмината натрия Na2O*11Al2O3.
Плотность - 3.90-3.95г/см3. Микротвердость - 19.6-20.9ГПа.
Как более твердый материал, используется в инструменте с твердой
связкой (керамика). Наиболее эффективен при обработке чугуна, нержавеющей
стали. Используется так-же, в шлифшкурке и свободном виде.
Электрокорунд хром-титанистый
Хром-титанистый электрокорунд получают в электродуговых печах
плавлением шихты, состоящей из глинозема или бокситов и легирующих
компонентов - оксида хрома и оксида титана. Материал из глинозема содержит
Cr2O3 не более 0.4%, TiO2 - не более 0.7% ; из бокситов : Cr2O3 -
0.1-0.5%, TiO2 - 1.7-3.5%. Легирование 2-мя компонентами улучшает
абразивные свойства материала. Используется в шлифшкурках и свободном
виде, и в инструменете для интенсивных режимов обработки конструкционных и
углеродистых сталей.
Электрокорунд циркониевый
Циркониевый электрокорунд получают из шихты глинозема и оксида циркония
в специальных наклоняющихся электродуговых печах, методом "на слив" с
последующим интенсивным охлаждением расплава, что позволяет получить
микрокристаллический материал с размерами первичных кристаллов до 50мкм.
Плотность - 4.05-4.15г/см3. Микротвердость - 22.6-23.5ГПа.
Циркониевый электрокорунд обладает высоким коэффициентом шлифования и
является самым эффективным материалом в обдирочных операциях с высокими
нагрузками и большим съемом металла,- производительность бакелитовых
обдирочных кругов из циркониевого электрокорунда более чем в 10 раз
превышает производительность кругов их электрокорунда нормального.
Карбид кремния черный
Карбид кремния SiC получают в электропечах при взаимодействии кремния и
углерода. Сырьем для карбида кремния служат кварцевый песок Si - не менее
99% и нефтяной кокс с массовой долей золы - не более 1%.
Плотность - 3.21г/см3. Микротвердость - 33ГПа.
Как очень твердый материал используется при обработке стекла, керамики,
железобетона, чугуна. Применяется при изготовлении инструмента с
различными типами связки и в шлифшкурке. Структура материала
("незасаливаемая") позволяет обрабатывать мягкие материалы - цветные
металлы, дерево, кирпич.
Карбид кремния зеленый
По своему химическому составу и физико-механическим свойствам карбид
кремния зеленый незначительно отличается от карбида кремния черного.
Сферокорунд
Сферокорунд получают методом раздува расплава глинозема и образования
полых корундовых сфер. Содержание Al2O3 в материале - не менее 99%.
Плотность - 3.90-3.95г/см3. Микротвердость - 19.6-20.9ГПа.
Сферокорунд используется для труднообрабатываемых материалов, таких как
жаропрочная сталь, мягких и вязких материалов, как кожа или резина.
Поддержание абразивных свойств материала происходит за счет разрушения
сфер в процессе шлифования и обнажения новых режущих кромок при малом
тепловыделении.
Формокорунд
Формокорунд получают методом экструзии высоковязкой водной суспензии
глинозема, последующей сушки и спекания при температуре 1700гр.С.
Содержание Al2O3 - 80-87%, Fe2O3 - не более 1.5%. Частицы имеют
цилиндрическую (С) или призматическую (Р) формы с размерами сечения -
1.2-1.8мм. и длиной - 3.8-8.0мм. Формокрунд используется в тяжелых
обдирочных операциях.
Монокорунд
Шлифзерно представлено монокристаллами, в отличии от нормального
электрокорунда, имеющего поликристаллическую структуру, что обеспечивает
высокую режущую способность, но и высокую стоимость этого материала.
Агрегат
Шлифовальный материал, полученный благодаря спеканию нескольких
абразивных зерен между собой.
Физико-механические свойства
материалов
Марка материала |
Плотность г/см3 |
Микротвердость ГПа |
Мех.прочность Н |
Абразивная способность г |
Режущая способность г/мин |
Насыпная плотность г/см3
|
25 |
8 |
М40 |
40 |
Карбид кремния зеленый |
3.15-3.25 |
32.4-35.3 |
11.0-14.7 |
0.09 |
0.057 |
1.49 |
Карбид кремния черный |
3.15-3.25 |
32.4-35.3 |
11.0-14.7 |
0.08 |
0.060 |
1.43 |
Электрокорунд нормальный |
3.85-3.95 |
18.9-19.6 |
8.6-19.9 |
0.06 |
0.036 |
1.78 |
Электрокорунд белый |
3.90-3.95 |
19.6-20.9 |
8.3-10.8 |
0.05 |
0.035 |
1.83 |
Электрокорунд хром-титанистый |
3.95-4.00 |
19.6-22.6 |
9.3-10.4 |
0.05 |
|
1.85 |
Электрокорунд циркониевый |
4.05-4.15 |
22.6-23.5 |
589 |
|
|
2.12 |
Зернистость абразивных материалов
Зернистость абразивов определяется размером зерен материала и зерновым
составом. Зерна добывают дроблением кусков охлажденного расплава
электрокорунда или карбида кремния и с помощью последующего разделения по
фракциям. Разделение зерен большого размера производится путем рассева
через сита, а микро зерен - при помощи гидравлической или воздушной
классификации .
В зависимости от размеров зерен, абразивы делятся на следующие виды :
Шлифзерно - 2000-160 мкм. ; Шлифпорошки - 125-40 мкм.;
Микропорошки - 63-14 мкм.; Тонкие шлифпорошки - 10-3 мкм..
Способы классификации, размеры и обозначение зернистости шлифматериалов
регулируются стандартом ГОСТ 3647-80.
Согласно ГОСТу зернистость микропорошков до 63 мкм. обозначается буквой
"М" плюс размер шлифзерна в микронах - "М63", зернистость шлифпорошков и
шлифзерна больших 63 мкм. обозначается номером, равным 1/10 размера зерна
в микронах, например : № 16 = 160 мкм.
Зерновой состав означает количество частиц основной фракциии, по
размеру которых определяют марку шлифзерна.
Содержание основной фракции в материале (%)
|
|
200-8 |
6-4 |
M63-M28 |
M28-M14 |
M10-M5 |
В |
Высшее |
|
|
60 |
60 |
55 |
П |
Повышенное |
55 |
55 |
50 |
50 |
45 |
Н |
Нормальное |
45 |
40 |
45 |
40 |
40 |
Д |
Допустимое |
41 |
|
43 |
39 |
39 |
Виды связок
Связка – собственно связующее вещество и наполнители. Вид связки имеет
определяющие значение для прочности и режимов работы абразивного
инструмента. В производстве абразивного инструмента применяют два вида
связок: неорганические (минерального происхождения) и
органические . К органическим связкам относятся: бакелитовая,
вулканитовая, глифталевая, эпоксидная, поливинилформалевая и полиэфирная.
Неорганические связки : (керамическая и магнезитная) обладают высокой
огнеупорностью, водостойкостью, химической стойкостью и относительно
высокой стойкостью.
В зависимости от поведения в процессе термической обработки они делятся
на плавящиеся (стекловидные) и спекающиеся (фарфоровидные). Общее название
– керамические (обозначаются «КПГ» и «КМ»). Существуют так же связки,
отверждающиеся без термической обработки (магнезитные-«М»). Плавящиеся
связки после остывания превращаются в стекло, спекающиеся расплавляются
только частично и по своему составу и состоянию близки к фарфору.
Для увеличения механической прочности абразивного инструмента
используются упрочняющие элементы. Прежде всего это металлические детали:
кольца, впрессованные в обдирочные круги; подложки для торцешлифовальных
кругов; фланцы для лепестковых кругов. В отрезных, зачистных и обдирочных
кругах, работающих при рабочих скоростях 80 м/с и выше в качестве
упрочняющего элемента используются диски, вырезанные из стеклосетки.
Используют стеклосетки с размером ячеек от 3 до 6 мм. и толщиной нити от
0,4 до 2 мм., пропитанные составами на основе фенолформальдегидной смолы.
Наличие упрочняющей сетки иногда указывается в маркировке круга буквой
«У». Известны случаи использования углеволокон для упрочнения инструмента.
Однако, низкая адгезия к органическим связкам и высокая стоимость
сдерживает на сегодняшний день их применение.
Керамическая связка
Керамическая связка чаще всего представляют собой многокомпонентную
смесь, составленную в определенных пропорциях из измельченных сырых
материалов: огнеупорной и керамических глин, плавней (полевого шпата,
борного стекла), талька и ряда других материалов. Недостатком керамической
связки является ее высокая хрупкость, вследствие чего круги на этой связке
не могут использоваться при ударных нагрузках (обдирочное, отрезное и
силовое шлифование). Относительно низкий предел прочности при изгибе не
допускает применение таких кругов для отрезных работ, так как они тонкие и
могут разрушиться от боковой нагрузки (изгибе).
Бакелитовая связка
Бакелит - полиоксибензолметиленгликольангидрид получают сочетанием в
различных пропорциях карболовой кислоты (фенола) и формальдегида. Варируя
этими компонентами получают смолу большим добавлением фенола или лак -
большим добавлением формальдегида.
Бакелит был запатентован в 1907 году и получил широкое распространение
как лак и как связующее, используемое в производстве корпусов изоляторов,
телефонных аппаратов, различных приборов. Именно открытием бакелита было
положено начало эры пластиков.
В абразивной промышлен y ости используются фенолформальдегидные лаки и
смолы. В Российской промышленности смолы обозначаются как:
СФЖ - смола фенольная жидкая и СФП - смола фенольная порошкообразная.
В изготовлении связок помимо смол используются различные наполнители
неорганического происхождения такие как криолит, пирит, алебастр и другие.
Абразивный инструмент на бакелитовой связке обладает высокой
прочностью, особенно на сжатие и ударной прочностью, превосходя по этим
показателям инструмент на керамике. Высокая прочность бакелитовой связки
позволяет абразивному инструменту работать при больших нагрузках и высоких
скоростях резания (при армировании стеклосеткой – до 80 м/с и выше). Так
же круги применяются для обдирочных и отрезных операций, при шлифовании с
большими нагрузками и съемом металла. К недостаткам следует отнести
невысокую теплостойкость – деструкция связки происходит при температурах
400 - 700 град.С, недостаточную устойчивость к воздействию щелочных
растворов, что ограничивает применение охлаждающих жидкостей (нежелательно
применение растворов, содержащих щелочи более 1,5%).
Вулканитовая связка
- многокомпонентная композиция ; основной компонент – синтетический
каучук. В качестве добавок: вулканизирующий агент – сера, ускорители
вулканизации (каптакс, тиурам и др.), минеральные и органические
наполнители регулирующие физико-механические и эксплуатационные свойства
абразивных инструментов и формовочные свойства массы. Инструмент на
вулканитовой связке обладает эластичностью и плотностью, поэтому может
использоваться как при обычных видах шлифования, так и при полирующих
операциях. Круги на вулканитовой связке в отличие от остальных могут быть
изготовлены очень тонкими (десятые доли миллиметра при диаметре до 150-200
мм.). Недостатком является низкая теплостойкость (250-300 град.С) и слабое
закрепление зерна в связке, что объясняет более низкую износостойкость
кругов в сравнении с бакелитовыми и керамическими.
Глифталевая связка
- продукт взаимодействия глицерина с фталевым ангидридом. Низкая
теплостойкость (120 град.С), невысокая твердость позволяет прииенять круги
на глифталевой связке только для процессов полирования при рабочей
скорости не выше 40 м/с.
Поливинилформалевая связка
- вспененный поливинилформаль. Другое название кругов на основе этой
связки – поропластовые. Используются для полирования с получением
шероховатости поверхности 0,63-1,0.
Эпоксидная и полиэфирная связки
В основном применяются для изготовления галтовочных тел, абразивных
изделий используемых во ращающихся барабанах и вибрационных контейнерах
для очистки поверхностей и снятия заусенцев деталей малого размера.
Абразив(ы) и абразивный материал(ы) именуются так же : шлифовальные
материалы, шлифовальное зерно, абразивное зерно, шлифзерно и т.п.
Свободные абразивы - абразивы используемые в свободном виде,
например, для пескоструйной обработки поверхностей, ручной обработки путем
нанесения на салфетку или на обрабатываемую поверхность, а так же
используемые в составе абразивных паст, гелей.
Абразивы в связке -
формованные изделия из смесей абразивного, связующего материалов и
наполнителей, с последующим отверждением или спеканием. Различают
следующие виды связок : керамическая или стекловидная, смолянистая,
вулканитовая и др.
Абразивные покрытия - абразивные зерна,
нанесенные на поверхность полотняной основы, например, бумажной, тканевой,
фибровой и др., и закрепленные на ее поверхности с помощью клеев и
смол.
Маркировка абразивного зерна
Маркировка шлифматериалов - это комбинация цифр и букв. Согласно ГОСТу
28818-90 электрокорунд нормальный имеет следующие обозначения : 12А, 13А,
14А, 15А. Чем выше число в префиксе маркировки, тем выше качество
материала, т.е. выше твердость за счет меньшего количества ненужных
примесей и выше режущая способность материала.
Электрокорунд белый обозначается : 22А, 23А, 24А, 25А.
Качество материала во многом зависит как от чистоты исходного сырья,
так и от способа производства.
Источником электрокорунда белого является глинозем - высокоалюминистое
сырье, продукт обогащения бокситовых глин (98-99% оксида алюминия). Т.н.
альфа-глинозем - почти стопроцентное сырье высшей степени очистки.
Получение из глинозема абразива высшего сорта (25А), обладающего высокой
твердостью и высокой режущей способностью, достигается за счет более
высокой температуры плавления и более быстрого охлаждения расплава,
благодаря чему кристаллы абразива становятся более "лучистыми" и при этом
более твердыми. Вспомним, что режущая способность абразивного зерна
определяется количеством режущих вершин. Более твердое зерно является и
более хрупким, поэтому высокосортный абразив лучше подходит для шлифшкурки
и прочих изделий с абразивным покрытием, в то время как материал низшего
сорта более пригоден в качестве свободного абразива для пескоструйного
шлифования.
Можно вывести шкалу, связав сортность абразивов и область применения по
принципу: от 12А до 25А - от СВОБОДНЫХ АБРАЗИВОВ до ИЗДЕЛИЙ С АБРАЗИВНЫМ
ПОКРЫТИЕМ (ШЛИФШКУРКИ).
Зерно марок 13А-15А эффективнее использовать в кругах при высоких
ударных нагрузках, например в отрезных и обдирочных кругах на бакелитовой
связке, и в другом инструменте и операциях, подразумевающих высокое
давление на обрабатываемую поверхность и/или объемное снятие материала.
Более хрупкие марки 22А-24А эффективнее используются в кругах на
керамической связке. В шлифшкурке и прочих изделиях с абразивным
покрытием, работа которых не связана с высоким давлением и направлена на
прецизионную обработку поверхностей, используют хрупкий материал с высокой
режущей способностью марок 24А-25А.
Хром-титанистый электрокорунд обозначается 95А.
Циркониевый электрокорунд обозначается 38А. Шлифзерно обладает
уникальным сочетанием прочности и высокой режущей способности, поэтому
используется в кругах для обдирочных операций с высокими ударными
нагрузками и объемным съемом материала. Режущая способность в 10 раз выше
чем у электрокорунда нормального в аналогичных операциях.
Сферокорунд - ЭС.
Монокорунд - 43А-45А.
Карбид кремния черный - 52С-55С.
Карбид кремния зеленый - 62С-65С. Получение высокосортного материала из
карбида кремния, как в случае с электрокорундом, достигается за счет
повышенной температуры плавления и быстрого охлаждения. Высокосортный
абразив из карбида кремния используется в основном в шлифшкурке.
Особенности классификации абразивных материалов
в зарубежных стандартах
Электрокорунд имеет общее название - fused aluminium oxide, дословно -
плавленый оксид алюминия. Электрокорунд нормальный и белый - brown fused
aluminium oxide и white fused aluminium oxide соответственно. Видно, что
названия ассоциируются с цветом материалов. Можно встретить такие
названия, как например : white corundum, white alumina (alumina -
глинозем).
Pink alumina - розовый оксид алюминия, хром-титанистый электрокорунд,
имеющий розовую окраску.
Ruby alumina или electroruby - рубиновый электрокорунд из оксида
циркония.
Общее название карбида кремния - silicon carbide, он-же - carborundum.
Black silicon carbide и green silicon carbide - соответственно черный и
зеленый карбид кремния.
|
Наименование и марки материала |
Примеры зарубежного обозначения
материала |

|
Электрокорунд нормальный 12A, 13A, 14A, 15A |
Brown fused aluminium oxide (corundum)
10A, 11A, A, ONA, TA |

|
Электрокорунд белый 22A, 23A, 24A, 25A |
White fused aluminium oxide (corundum)
33A, 38A, WA, OBA, EK |

|
Электрокорунд хром-титанистый 95A |
Chromium-titanium corundum (pink corundum)
66A, 88A |

|
Циркониевый электрокорунд 38A |
Zirconium corundum (electroruby) 77A, ZC
|

|
Карбид кремния черный 52C, 53C, 54C, 55C |
Black silicon carbide (carborundum) 21C, 37C, 55C,
BC, SIC, SC21, 1C |

|
Карбид кремния зеленый 62C, 63C, 64C, 65C |
Green silicon carbide (carborundum) 22C, 39C, 66C, C,
SICg, SCg, 4C |
Сортность абразивных материалов имеет строгую привязку к области
применения. В классификации FEPA (Federation of european producers of
abrasives) шлифзерно разделяется на классы :
F ( First grade , bonded abrasives )- первый сорт, абразивы в связке
(шлиф.круги и др.), и P ( Premium grade , coated abrasives ) - высший
сорт, абразивные покрытия (шлифшкурка и др.).
В американской классификации приняты следующие обозначения : B -
(blasting) шлифзерно для пескоструйной обработки ; R - (rigid)
шлифзерно низкой плотности для шлифовальных кругов и др. абразивов в
связке ; L - шлифзерно высокой плотности для шлифшкурки и проч.
абразивных покрытий.
Зернистость абразивных материалов обозначается буквой и числом ; буква
указывает на сорт материала, число - это количество зерен на одном
линейном дюйме сита. Например - F120, соответствует №10 по российской
классификации. Очень приблизительно номер по FEPA можно рассчитать по
формуле:
Размер по FEPA = 2,54 * 1000 / 2N,
где N - размер шлифзерна по российской
классификации.
В силу того, что российские стандарты позволяют большие допуски при
рассеве и не учитывают сорта материала, четкого соответствия между
отечественной и зарубежной классификацией нет. Кроме этого существуют
небольшие различия в зернистости сортов F и P. К рассеву материала сорта P
предъявляются более строгие требования, подразумевающие более четкую
селекцию по зерновому составу с минимальными допусками. Так же есть
различия в определении размеров зерен. Сорт P отличается от F
"лучистостью", наличием большего числа режущих вершин, т.е. занимая
одинаковый объем зерно P весит несколько легче зерна F. Поэтому шкала
зернистости по сорту P более условна - номера зерен несколько занижены по
отношению к реально занимаемому объему для приведения в соответствие с
весом, основным параметром, учитываемом в производстве изделий из
абразивов.
Обозначение зернистости шлифматериалов из оксида
алюминия и карбида кремния в соответствие с ГОСТ и зарубежными стандартами
для щлифовальных кругов
ГОСТ 3647-80, 28818-90 |
FEPA 42-1993, ISO 8486 |
Зернистость |
Размер (микрон)
|
Зернистость |
Размер (микрон)
|
– |
– |
F4 |
4890 |
– |
– |
F5 |
4125 |
– |
– |
F6 |
3460 |
– |
– |
F7 |
2900 |
240 |
2800-2000 |
F8 |
2460 |
200 |
2400-2000 |
F10 |
2085 |
160 |
2000-1600 |
F12 |
1765 |
140 |
1600-1400 |
F14 |
1470 |
120 |
1400-1200 |
F16 |
1230 |
100 |
1200-1000 |
F20 |
1040 |
80 |
1000-800 |
F22 |
885 |
70 |
800-710 |
F24 |
745 |
60 |
700-600 |
F30 |
625 |
50 |
600-500 |
F 36 |
525 |
40 |
500-400 |
F 40 |
438 |
32 |
400-320 |
F 46 |
370 |
30 |
320-300 |
F 54 |
310 |
25 |
300-250 |
F 60 |
260 |
20 |
250-200 |
F 70 |
218 |
16 |
200-160 |
F 80 |
185 |
14 |
160-140 |
F 90 |
154 |
12 |
140-120 |
F 100 |
129 |
10 |
120-100 |
F 120 |
109 |
8 |
100-80 |
F 150 |
82 |
6 |
80-60 |
F 180 |
69 |
М 63 |
63-58 |
F 220 |
58 |
М 58 |
58-50 |
F 230 |
53.0±3 |
М 50 |
50-40 |
F 240 |
47.5±2 |
М 40 |
40-28 |
F 280 |
36.5±1.5 |
М 40 |
40-28 |
F 320 |
32.8±1.5 |
М 28 |
28-20 |
F 360 |
29.2±1.5 |
М 20 |
20-14 |
F 400 |
17.3±1 |
М 14 |
14-10 |
F 500 |
12.8±1 |
М 10 |
10-8 |
F 600 |
9.3±1 |
М 8 |
8-5 |
F 800 |
6.5±1 |
М 5 |
5- |
F 1000 |
4.5±0.8 |
– |
– |
F 1200 |
3.0±0.5 |
Стандарты и ТУ для шлифматериалов
1 |
Материалы шлифовальные из корундовых и наждачных руд. Технические
условия. |
ТУ 2-036-972-85 |
2 |
Материалы шлифовальные из карбида кремния. Технические условия.
|
ГОСТ 26327-84 |
3 |
Материалы шлифовальные из карбида кремния черного марки 51С.
Технические условия. |
ТУ 2-036-972-85 |
4 |
Материалы шлифовальные из электрокорунда. Технические условия.
|
ГОСТ 28818-90 |
5 |
Материалы шлифовальные из электрокорунда белого. Технические
условия. |
ТУ 2-036-350-74 |
6 |
Материалы шлифовальные из электрокорунда белого. Технические
условия. |
ТУ 2-036-288-86 |
7 |
Материалы шлифовальные из электрокорунда белого |
ТУ 2-036-314-88 |
8 |
Материалы шлифовальные из хром-титанистого электрокорунда.
Технические условия. |
ТУ 2-036-0221066-007-90 |
9 |
Материалы шлифовальные из хром-титанистого электрокорунда |
ТУ 2-036-849-85 |
10 |
Материалы шлифовальные из циркониевого электрокорунда.
Технические условия. |
ТУ 2-036-0221841-006-90 |
11 |
Материалы шлифовальные из сферокорунда. Технические условия.
|
ТУ 2-036-0221841-006-90 |
12 |
Материалы шлифовальные. Классификация. Зернисость и зерновой
состав. Методы контроля. |
ГОСТ 3647-80 |
|